Für viele Prüfaufgaben ist luftgekoppelter Ultraschall ein vielversprechender Ansatz. Entdecken Sie die Diversität der Anwendungsmöglichkeiten in der Prüfbeispielgalerie.
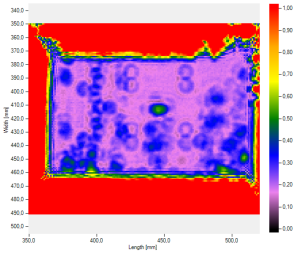
Leiterplatten (PCB)
Leiterplatten sind als Träger für elektronische Bauteile die Basis jedes elektronischen Gerätes.
Sie bestehen üblicherweise aus einer Mehrlagenstruktur von leitfähigen Bereichen (Leiterbahnen aus Kupfer ) und isolierenden Schichten aus faserverstärktem Kunststoff.
Währende der Herstellung der Leiterplatte kann es prozessbedingt zu Störungen dieses Mehrlagenaufbaus kommen. Auch durch die mechanische Bearbeitung, z. B. durch das Einbringen von Löchern für Befestigungen oder Durchkontaktierungen kann es zu einer Vorschädigung des Lagenaufbaus kommen.
Bei der Bestückung der Leiterplatten mit den Bauelementen wird das Löten zunehmend in einem Reflow-Prozess durchgeführt. Dabei wird die gesamte Leiterplatte bis zur Löttemperatur erwärmt. Bei dieser thermischen Belastung kann es in einer vorgeschädigten Leiterplatte zum Ausbilden von Delaminationen kommen, die im ungünstigen Fall zu Kurzschlüssen oder anderen Beeinträchtigungen der Funktionsweise führen. Diese müssen nicht immer sofort erkennbar sein, sondern können erst im späteren Betrieb zum Ausfall der Leiterplatte führen.
Mit der luftgekoppelten Ultraschallprüfung können solche Delaminationen in verschiedenen Stufen des Herstellungsprozesses detektiert werden. Die Leiterbahnen aus Kupfer, und selbst bereits auf der Leiterplatte befindliche Bauelemente sind dabei nicht kritisch. Sie sind entweder nicht sichtbar (Kuferleiterbahnen) oder und können durch einen Vergleich mit einer Referenzplatte deutlich von Delaminationen unterschieden werden.
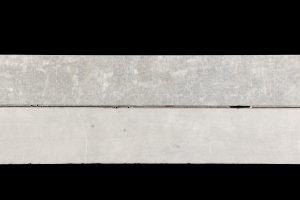
Laserschweißnaht am Blech
Die Prüfung von Metallen ist eine besondere Herausforderung, da wegen der höheren akustischen Impedanz noch mehr Schallenergie an der Oberfläche reflektiert wird als bei Kunststoffen.
In der Automobilindustrie und im Schienenfahrzeugbau werden Bleche häufig automatisch geschweißt. In der Prozesskontrolle sollte unmittelbar hinter dem Schweißroboter geprüft werden, um auf Unregelmäßigkeiten möglichst sofort reagieren zu können. Für eine berührende Ultraschallprüfung müssen die Bleche aber erst abkühlen. Mit der Lamb-Wellen-Methode kann jedoch berührungslos und auf einer Seite der Bleche geprüft werden. Dabei wird durch eine Schrägeinschallung auf einer Seite der Schweißnaht im Blech eine Plattenwelle angeregt. Diese auch als Lamb-Welle bezeichnete Welle gibt bei der Fortbewegung ständig Schallwellen in die Luft, die auf der anderen Seite der Schweißnaht mit einem Empfänger detektiert werden.

GFK – Windradflügel
Die Flügel von Windrädern sind zum Teil aus mehreren Zentimeter dickem glasfaserverstärkten Kunststoff gefertigt. Die mehrlagige Struktur dämpft Ultraschallwellen in hohem Maße.
An einem Probekörper, der in Form eines Keils aus einem Windradflügel ausgeschnitten wurde, sollte die Dickenabhängigkeit der Luftschallprüfung getestet werden. Bei unterschiedlichen Probendicken verringert sich die Signalstärke mit zunehmender Dicke, da die Dämpfung zunimmt. Außerdem ändert sich die Signallaufzeit. Diese geometrischen Einflüsse können zu Artefakten im Prüfbild führen, welche dann von den eigentlichen Materialfehlern unterschieden werden müssen.
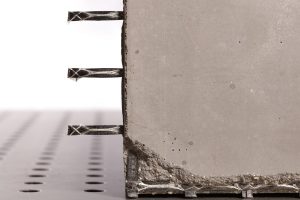
Textilbeton
Textilbeton oder auch faserverstärkter Beton ist ein neuartiger Baustoff, bei dem die klassische Stahlbewehrung durch eine Struktur aus Faser- oder Faserbündeln ersetzt wurde.
Diese Fasern können Kohle-, Glas- oder mineralische Fasern (wie Basalt) sein. Der Begriff Textil wird verwendet, da sie häufig zu Matten oder Gelegen verwebt oder geflochten sind – wie bei Textilien üblich. Aus Textilbeton können wesentlich leichtere Betonstrukturen gebaut werden. Das verringert einerseits den Materialeinsatz. Andererseits stellt es höhere Anforderungen an die Herstellung, da die Lage der Faserstruktur genau stimmen muss. Eine Aufgabenstellung für die zerstörungsfreie Prüfung ist daher die Detektion des Fasergeleges und möglichst eine Tiefenmessung unter der Decklage.
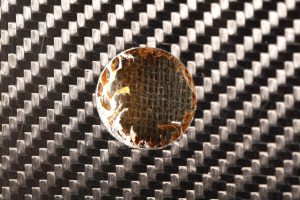
Wabe
Ein typisches Leichtbaumaterial ist eine Verbundwerkstoffstruktur aus Decklagen und einer Wabenstruktur zur inneren Versteifung. Fehler oder Schädigungen treten meist im Inneren auf und sind von außen nicht sichtbar.
In diesem Beispiel bestehen die äußeren Decklagen aus einer mehrlagigen CFK-Platte von ca. 1 mm Dicke. Als Kern wurde eine Aramid-Wabe verwendet, die ca. 10 mm dick ist. Typische Fehlerbilder sind entweder Herstellungsfehler wie unzureichende Verklebungen von Wabe und Kern oder Schädigungen, die zum Beispiel nach einem Stoß (Impact) und anschließender weiterer Belastung auftreten können. Im Gegensatz zum Metall entstehen keine Beulen im Material, sondern eventuell feine, kaum sichtbare Risse oder langfristig Ablösungen der Wabenstruktur im Inneren. Insbesondere letzte Schädigung ist kritisch, da sie nicht durch eine Sichtprüfung erkannt wird.
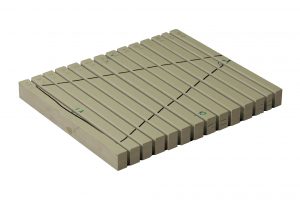
Faserverstärkter Kunststoff
Bei der Herstellung von mehrlagigen faserverstärkten Kunststoffen dürfen im Herstellungsprozess keine Poren im Inneren auftreten, da diese die mechanische Festigkeit des Materials negativ beeinflussen.
Diese Probekörper bestehen aus teilweise mehr als 100 Lagen und weisen dabei eine Gesamtdicke von bis zu 130 mm auf. Eine solche Probe kann auf Grund ihrer sehr hohen Dämpfung mit konventionellem Ultraschall nicht mehr geprüft werden. Bei der Fertigung können im Inneren zwischen den Lagen Poren auftreten. Diese haben meist eine linsenförmige Gestalt mit Durchmesser unter 3 mm und einer Höhe von weniger als 1 mm. Sie sind von außen nicht sichtbar, verringern aber die Festigkeit, wenn sie in größerer Anzahl auftreten.
Sie müssen den Inhalt von reCAPTCHA laden, um das Formular abzuschicken. Bitte beachten Sie, dass dabei Daten mit Drittanbietern ausgetauscht werden.
Mehr Informationen